As has been the case for many of the critical rare metals in our investment universe, rhenium has been impacted by the Covid-19 crisis both in terms of mining production (rhenium being a by-product of a by-product), and in terms of demand (mainly from the aeronautical sector). Nevertheless, despite the current environment of uncertainty, there is little doubt that the physical properties of rhenium will make it increasingly essential for future aeronautical technologies, which will require ever stronger and ever lighter superalloys.
Meanwhile, the price of rhenium currently stands at a historically low level.
We believe that strong demand should, in the long run, outweigh the downside effects of an aircraft industry that is currently in crisis. To invest in rhenium could be a particularly interesting idea in the near future, and this is why we have decided to make it the subject of our next two articles.
What is rhenium?
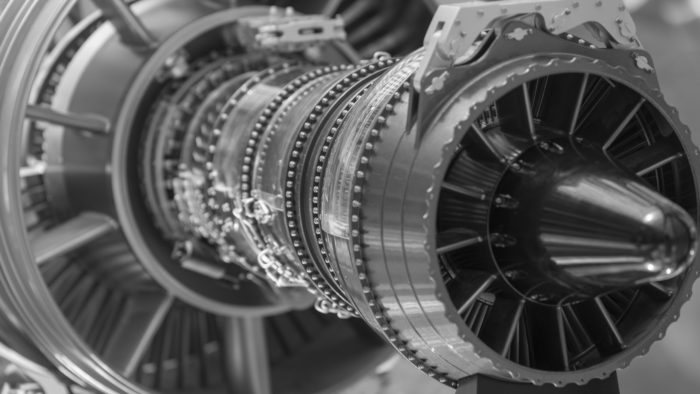
Rhenium (chemical symbol Re) is a transition metal of atomic number 75. Rhenium is distinctive by its rarity, the difficulty of its extraction, and the unique properties that it lends to technological products. It is also the only mined metal to be a by-product of a by-product,. Rhenium is a very dense metal (21.02 g / cm3), and has a very high melting point of 3185 ° C (only surpassed by that of tungsten and carbon), which gives it exceptional refractory properties.
Rhenium is one of the rarest elements in the earth’s crust; the 77th in order of abundance. Its mass content in the earth’s crust is between 0.7 and 7 ppb (parts per billion, 1 ppb being equivalent to 1 mg / ton). Its main ore is molybdenite, MoS2, found in North and South America, but rhenium can also be found in sedimentary copper deposits in Kazakhstan, Poland or Armenia. Rhenium is mainly a by-product of molybdenum, which is itself mainly by-product of copper.
The annual production of primary rhenium is around 50 tons per year, to which can be added around 20 tons from recycling. Chile is the main producer of rhenium and represented 56% of world production in 2018. Next come the United States and Poland with 18% and 14% respectively.
The history of rhenium
Rhenium was discovered relatively late. Mendeleev had predicted its existence in 1871 when constructing the periodic table of the elements, leaving two empty spaces under manganese. However, the actual experimental discovery of those two elements proved difficult. Indeed, with its low position in the periodic table, rhenium was the last stable, non-radioactive element naturally present in the earth’s crust to be discovered. Rhenium was first isolated in 1925 in Germany, by W. Noddack, I. Tacke and O. Berg, in a platinum ore, where it emerged as an impurity. Rhenium was named after the Rhine – Rhenus, in Latin.
Rhenium compounds
The rhenium market is divided into two main compounds: Ammonium perrhenate (APR), with the formula NH4ReO4, and rhenium metal:
- APR is synthesized via the pyrometallurgy of concentrates of molybdenite, which is an ore rich in molybdenum. When roasting molybdenite at around 600 ° C, gases containing rhenium oxide are formed. The oxide is then treated and recovered by elution with ammonia (NH4) to form the APR. The recovery rate for rhenium is approximately 60%. APR is a rhenium compound directly used as a catalyst in petrochemicals, but it is also an intermediate product for the synthesis of rhenium metal.
- The APR can be hot-reduced with hydrogen to form rhenium metal. Once the rhenium powder is obtained, rhenium metal pellets are produced by sintering the powders. The purity of the metal is then 99.9%. Rhenium metal can then be incorporated into various metal alloys, superalloys in particular.
Rhenium applications
Over the last thirty years, rhenium has been mainly used in manufacturing high performance superalloys as well as in developing catalysts that combine platinum and rhenium, and are intended for the petroleum industry.
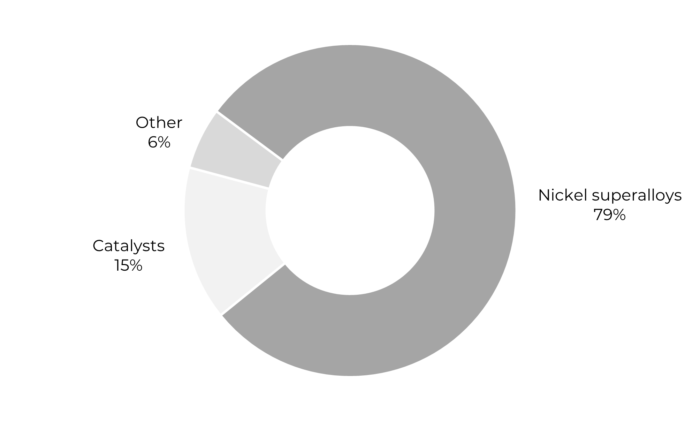
Source: USGS, 2017
Superalloys account for nearly 80% of rhenium demand and are widely used in the aeronautical sector. These alloys provide the exceptional levels of mechanical and thermal resistance needed in high-temperature operating conditions, as well as increased resistance to corrosion, creep and wear. There are many superalloys that contain iron, nickel and cobalt but their specific compositions can differ widely. Rhenium, on the other hand, is only used in nickel-based superalloys. These are the alloys that make up the single crystal turbine blades of aeronautical turbojets or industrial gas turbines. Those components undergo significant thermal stresses in service because they are so close to the combustion zone. The table below shows the compositions of certain nickel-based alloys.
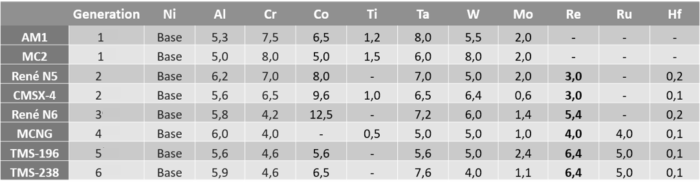
Source : Franck Nozahic, thèse 2016, DOI: 10.13140/RG.2.2.28248.60169
Rhenium content in nickel superalloys has increased steadily over successive generations to reach 6.4% of their total mass. While the addition of rhenium significantly boosts the mechanical properties of superalloys, excessive levels can nonetheless have the opposite effect by deteriorating the characteristics of the alloy. The challenge for new generations of nickel superalloys is to optimise the contents of the various metals in the components, and of rhenium in particular.
The use of rhenium is also essential for the defense sector. Indeed, the temperatures reached by military engines are higher than those for civilian aircraft, at 1600°C, and their consumption of rhenium is consequently higher. Roskill estimates the share of rhenium used for military aircraft at 37%, while the military aviation market represents only 11% of the total aviation market.
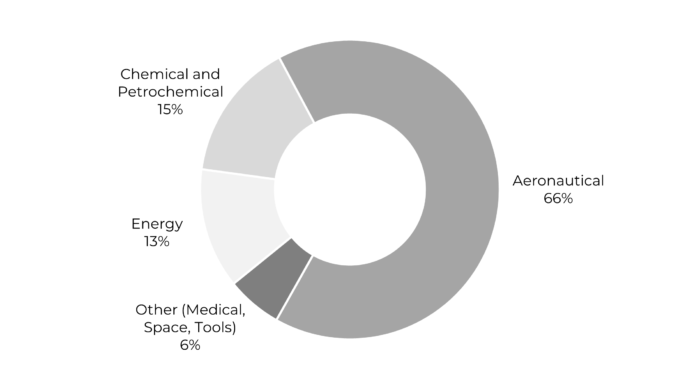
Source: Prometea, Rhenium factsheet, 2020
So approximately 80% of rhenium demand is accounted for by superalloys in aircraft engines as well as by gas turbine power generation. And another sector that requires rhenium is the petrochemical industry, where rhenium is the element of choice for certain catalysts.
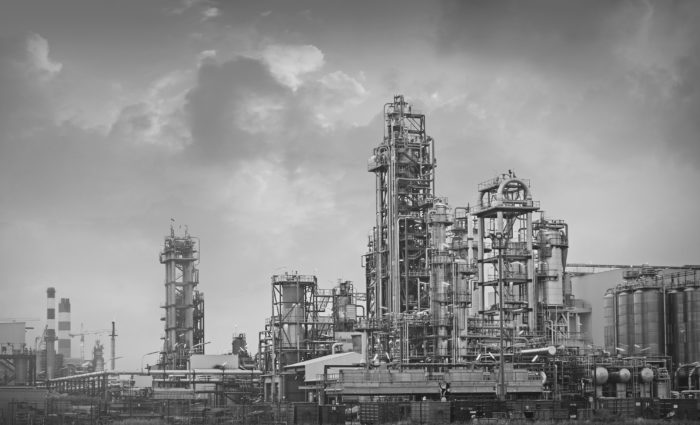
Indeed, catalysts that combine platinum and rhenium are widely used in the process of refining crude oil to increase the octane number in fuels. Numerous petroleum derivatives can be obtained in particular with gasoline and diesel (gasoline reaching the highest octane level), but also with benzene, toluene, and xylene. The presence of rhenium in platinum catalysts makes it possible to raise working temperature ranges and thereby to allow more efficient refining. Rhenium also improves the recovery capacity of catalysts which can then be reused on further refining cycles.
Finally, a few remaining applications use rhenium in much smaller quantities for its refractory properties . Those applications represent around 6% of the rhenium market:
- Rhenium is used in the resistors of electric furnaces, and in the filaments of incandescent lamps.
- Thermocouples used at high temperatures of up to 2800 ° C require tungsten and rhenium alloys.
- Alloys combining rhenium with tungsten or molybdenum are used in the anodes of X-ray tubes in radiography / the medical sector.
Should we be investing in rhenium? That question will be the focus of our next article, in which we will examine the rhenium market, and discuss any outlooks that our analysis can offer to potential investors.
Sources
- L’élémentarium, fiche de l’élément rhénium, 2019.
- BRGM, Panorama 2010 du marché du rhénium, Septembre 2011.
- Argus Metal, 2020.
- USGS, 2020.
- Lipmann Walton & Co Ltd, Rhenium, 2020, https://www.lipmann.co.uk/rhenium.
Dear CDMR:
Our firm is looking to invest in Rhenium (Re) 75. Please send a prospectus with all
relative contact information for investors to:
Capital Asset Associates, LLC
3 Germay drive, Ste 5
Wilmington DE 19804
USA
email: captialassetassocaites@protonmail.com
Thank you,
Vincent Lewis
CEO, CFO